The six (6) steps of the continuous improvement process are: Select the appropriate process for improvement.
Pin von Katie Olson auf Personal development Präsentieren
The plan stage identifies issues, problems or opportunities to improve in a process/product.
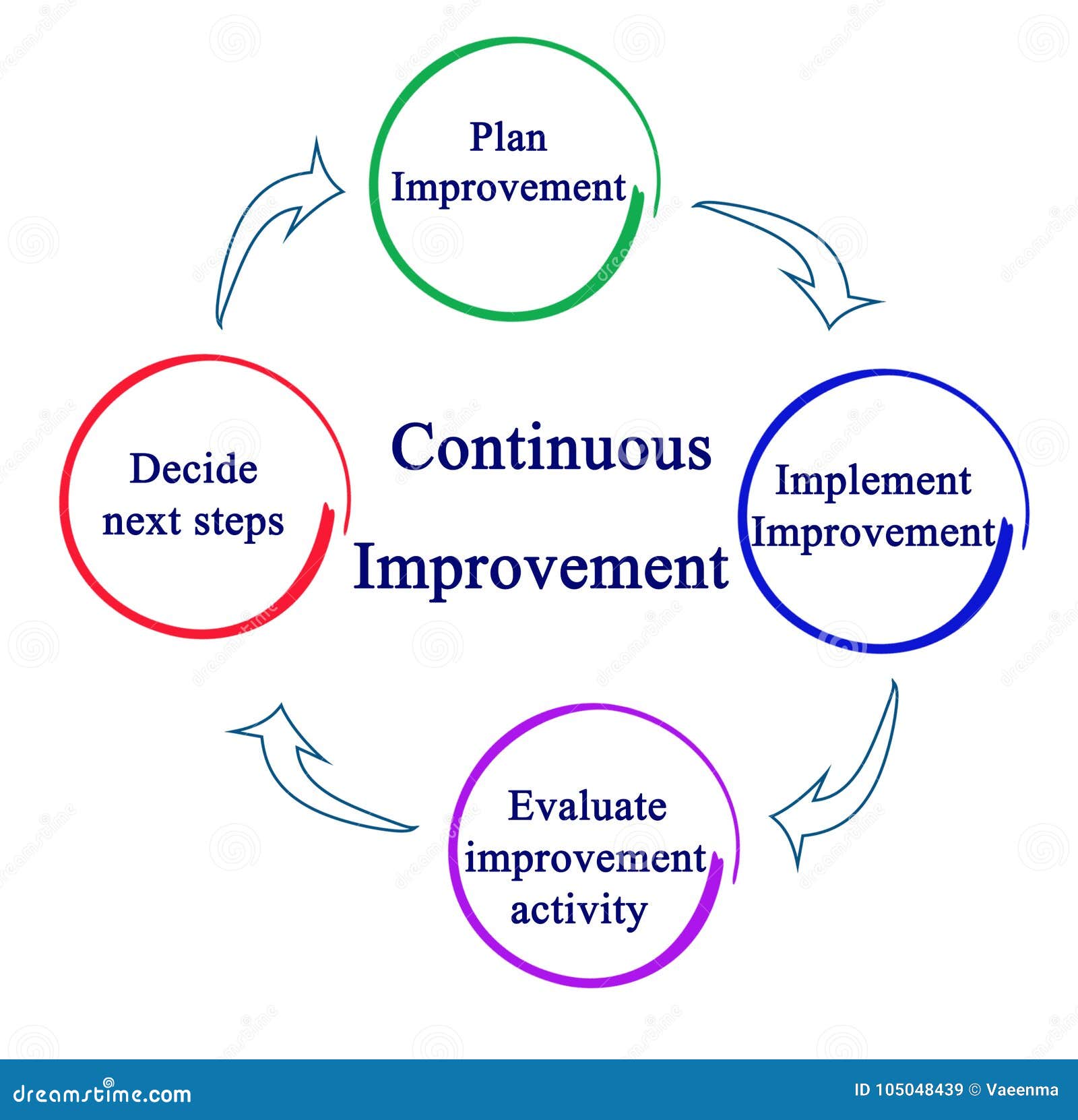
The six steps of continuous process improvement. A systematic identification of problems in workflows and processes. By definition, continuous process improvement (cpi) is the act of implementing improvements to a product, service or process. The kaizen cycle, also called the pdca or deming wheel, is the quintessential continuous process improvement technique.
Plan and implement actions that correct the root cause(s). Process improvement is the proactive task of identifying, analyzing and improving upon existing business processes within an organization, with the goal of improving process efficiency. Examine whether the change has the desired effect.
This is the most important stage, and can take up to 50% of the entire pdca cycle. Continuous improvement is the ongoing practice of process improvement; And yet, they all share the 6 principles of the continuous improvement model.
In the quality circle, the actual. For this purpose, internal workshops are usually held in the form of quality circles. This process stems from the 1920’s early improvement model plan, do, see developed by the statistician walter shewhart.
These are conducted by a continuous improvement manager or coach. This initiates a kaizen cycle. Select the appropriate process for improvement.
Organizations that focus on continuous improvement become. Continuous process improvement (cpi) is the practice of making incremental changes to your business processes to improve efficiency and quality. Identify and verify the root cause (s).
Six sigma, lean, and lean six sigma are all focused on improving processes to create more value to the customer. Some tools or methodologies that can be useful for continuous improvement processes are: Identify and verify the root cause(s).
A cip is a systemized way of constantly looking for ways to improve your productivity and workflow. You don’t just optimize a certain process once, pat yourself on the. Plan and implement actions that correct the root cause(s).
One may also ask, what are continuous improvement activities? This is paramount to the effectiveness of continuous improvement. All of the above methodologies have been developed for different types of organizations with different goals in mind.
One great way to make continuous improvement an ingrained part of your work process is to implement a continuous improvement (cip) in the workplace. Continuous process improvement is sometimes also known as ‘continual process improvement’. These are iterative processes in nature.
Learn vocabulary, terms, and more with flashcards, games, and other study tools. These test case programs are completely invested into. The team needs to identify and agree.
We lack a consistent, structured approach to analyzing challenges and developing solutions. A group of processes or steps leads to an execution outcome. The six (6) steps of the continuous improvement process are:
Lean refers to removing waste in any process, while six sigma refers to optimizing a specific process. It’s a process improvement that is woven into the fabric of daily work, as opposed to. A typical organization will have only 6 to 10 execution outcomes.
Companies that have seen achievement begin with smaller scale pilot projects before getting the whole organization included. Kaizen (“kai” means “change” and “zen” means good). Select the appropriate process for improvement.
In this way, what are the steps of process improvement? Conducting an objective investigation of your current systems and processes is imperative. The deming cycle is a systematic process aimed at improving services or products by gathering valuable knowledge and learnings.
Not to be confused with business process reengineering (bpr), continual improvement invites you to make. The first step is defining what done means. Identify and verify the root cause(s).
In the first step, the continuous improvement process begins with opportunity scouting: Select the appropriate process for improvement. Then the next steps lead to the next execution outcome.
Lean focuses on reducing waste from a system, while six sigma’s goal is to improve quality. The six (6) steps of the continuous improvement process (cip) step 1: Make a change plan and look for ways to improve.
The cycle is comprised of four stages: Develop a clear inquiry that addresses your proposed “fix.”. Start studying the six steps of the continuous process improvement.
Each stakeholder on the team needs to be aware of, and in agreement with the business objectives. Confirm the actions taken to achieve the target. These changes can either be incremental (over time) or breakthrough (all at once).
Implement across the organization and process if effective. Continuous process improvement (cpi) is a methodology that focuses on continuous improvements to products, services, or processes. Plan, do, check, and act.
Starting small is one of the best steps in continuous improvement process in case you’re an organization new to continuous improvement. Changes or improvements can be done gradually or in one go.
What is the use of histogram with respect to quality control? The pareto chart will illustrate total defects and also defect by type.
Histogram and Normal Distribution Curve of Health Care Workers' Scores
The resource histogram is a tool that is often used by the project management team and or as a means of providing a visual representation to the team and to all of those interested parties.

What is histogram used for by improvement teams. Contrast is defined as the difference in intensity between two objects in an image. The histogram has often been mentioned as one of several quality improvement and management tools used for determining productivity as well as profitability. Open the data analysis box.
Resource histograms help project managers with resource planning and quality management. Project management software has made resource histograms somewhat obsolete, but it still can show up in. A histogram enables a team to recognize and analyze.
The team should take care to validate that this metric is really indicative of the process. What is a histogram used for by improvement teams? A histogram takes continuous (measured) data like temperature, time, and weight, for example, and displays its distribution.
When used in process capability studies, histograms can display specification limits to show what portion of the data does not meet the specifications. If the team is improving throughput, then the item being measured may be defects.a common tool to use for this analysis is a pareto chart. More specifically, a histogram is a type of bar chart that graphs the frequency of occurrence of continuous data, and will aid you in analyzing your data.
There are many different ways to organize data and build histograms. Learn how histograms help planners and project teams weigh their options and alternatives. Each bar typically covers a range of numeric values called a bin or class;
Superimposed or adjacent histograms can be used to compare two time periods to evaluate changes in performance. A resource histogram is a statistical tool used to manage resources. A histogram is the most commonly used graph to show frequency distributions.
Commonly used to present quality improvement data, histograms work best with small amounts of data that vary considerably. Looking for the use of histogram in quality control of project management. In the most common form of histogram, the independent variable is plotted along the horizontal axis and the dependent variable is plotted along the vertical axis.
Additionally, from the lens of a pmp credential holder, a resource histogram is a specific use of the tool using project resource data. The team should identify the metric that is representative of the process performance. The histogram, a bar graph, provides a means to display variable data measured on a continuous scale for metrics such as time, temperature, weight, and speed.
In this example, the ranges should be: Histograms can also help users identify potential improvements in processes of care. Histograms measure continuous, quantitative data:
In that way histograms are a powerful quality tool. You can safely use any of them as long as you follow the basic rules. If the contrast is too low, it is impossible to distinguish between two objects, and they are seen as a single object.
However, there is a key difference: Dispersion of the data can produce a wide variety of histogram shapes, each. A histogram allows improvement teams and stakeholders to evaluate patterns in performance and visualize the distribution of data.
It’s a historical bar chart diagram that defines a resource allocation schedule. Enter the relevant input range and bin range. Explore how you can actually achieve that with histogram.
A histogram is a special type of bar chart used to display the variation in continuous data like time, weight, size, or temperature. The main focus of the histogram interpretation is the resulting shape of a distribution curve superimposed on the bars to cross most of the bars at their maximum height. If your data is from a symmetrical distribution, such as the normal distribution, the data will be evenly distributed about the center of the data.
Since the histogram is such an important tool, it can have many uses, which this article explains by way of a sample set of data and its histogram presentation. A histogram is a quality control tool that graphically displays a data set. When used in process capability studies, histograms can display specification limits to show what portion of the data does not meet the specifications.
What is a histogram used for by improvement teams? Download the corresponding excel template file for this example. It looks very much like a bar chart, but there are important differences between them.
The picture a histogram provides about the distribution of your process outcomes can help you determine what or where the problem might be. A histogram is a chart that plots the distribution of a numeric variable’s values as a series of bars. Basic tools for process improvement 6 histogram how is a histogram constructed?
Data that can be counted. Histograms are very useful tools for project management teams in their quests for quality or process improvements. Bar charts measure categorical data:
The data appears as colored or. Commonly used to present quality improvement data, histograms work best with small amounts of data that vary considerably. Often, summary statistics alone do not give a complete and informative picture of the performance of a process.
Let us create our own histogram. A frequency distribution shows how often each different value in a set of data occurs. A bar’s height indicates the frequency of data points with a value within the corresponding bin.
Data that can be split into different categories or types. Specifically speaking, the resource histogram is specifically a bar chart that is used for the purposes of displaying the specific amounts of time that a. This can be found under the data tab as data analysis:
The histogram above shows a frequency distribution for time to.
The 7 quality tools were first conceptualized by kaoru ishikawa, a professor of engineering at the university of tokyo.they can be used for controlling and managing quality in any organization. The tools described include clinical audit.
Project Management Total Quality Management, Tools and Techniques for TQM
It can help you to implement continuous improvement throughout your organization using a structured.
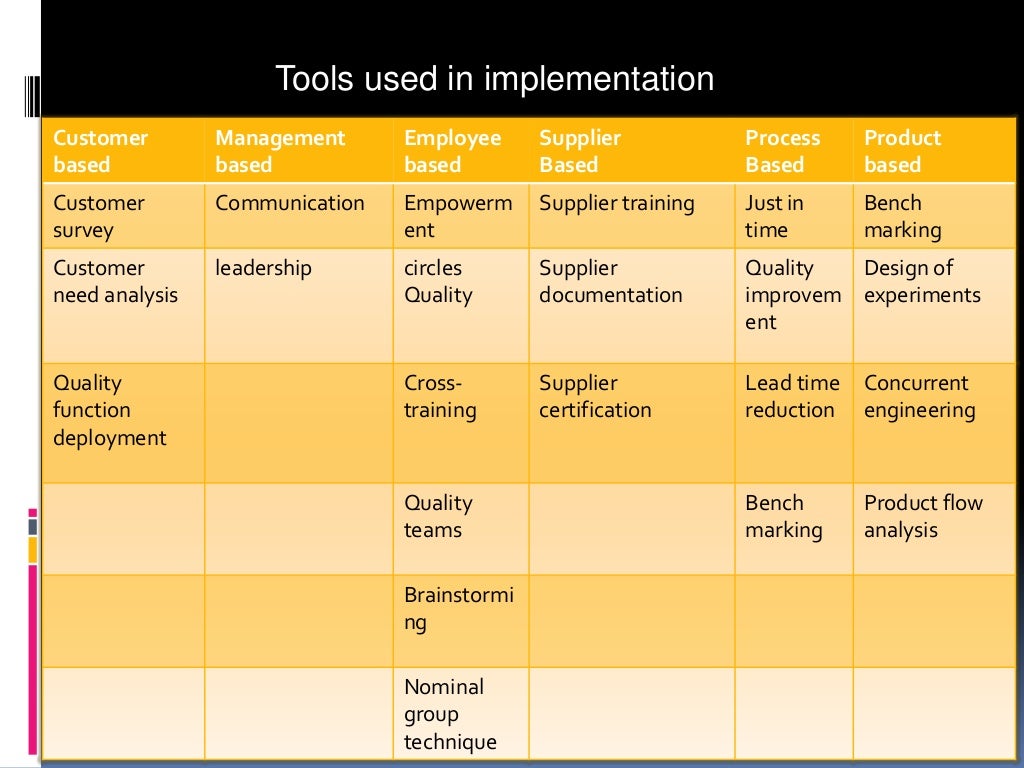
Tools and techniques used for quality improvement. The pdca cycle (short for plan, do, check, act) provides you with a systematic approach to testing different ideas and hypotheses. Quality improvement requires five essential elements for success: This is a technique in which the focus is one the quality improvement of the product by removing or eliminating the defects which are a hurdle in the quality.
To achieve continuous improvement and customer satisfaction,. 8 rows 7qc tools through pdca cycle. Reference the tools and techniques paragraph under assess quality items for more information.
Total quality management ( tqm) is a popular approach to quality in a business. 7 basic quality tool templates. The 7 basic quality tools are essentially techniques used to identify and fix issues.
The sigma basically is the greek name of the. Six sigma is a very old method of quality management and used widely in industries like mechanical and electrical works. They show how many times each particular value occurs, and.
Flowcharts describe a process in as much detail as possible by graphically displaying the steps in proper. Every project manager wishes to deliver the project with high quality and these seven basic quality management tools. Check sheets help organize data by category.
It seeks to improve quality and performance which will meet or exceed customer expectations. Histograms are a type of bar charts that depict the distribution of variables. Quality management tools and techniques control charts.
This guide is an update from the 2015 guide to qi methods and incorporates root cause analysis as a qi tool. Control charts measure the results of processes over time and display the results in the form of a graph. The 7 basic quality tools are, essentially, graphical techniques used to identify & fix issues related to product or process quality.
Here’s an overview of the six most popular and effective continuous improvement tools available. In fact, techniques and tools are vital to support and develop the quality improvement process ( bunney and dale, 1997; Fostering and sustaining a culture of change and safety, developing and clarifying an.
The 7 basic tools of quality (or 7 qc tools) were conceptualized for the first time by kaoru ishikawa, a professor of engineering at the university of tokyo. Just download the spreadsheets and begin entering your own data. These tools and techniques are similar to those described in the assess quality items section of this document.
With the seven basic tools of quality in. It’s used with a team to generate ideas, quickly and effectively. The tools and techniques most commonly used in process improvement are:
This can be achieved by integrating the quality functions and key processes throughout the company. 7 basic quality improvement tools flowcharts. It brings together ten other quality improvement tools providing an overview of each and practical advice on how and when to implement them, with illustrative case examples.
Whatever the acronym of the method (e.g., tqm, cqi) or tool used (e.g., fmea or six sigma), the important component of quality improvement is a dynamic process that often employs more than one quality improvement tool. According to some experts, this is the best tool for documenting the processes. One core component of tqm is the principle of continuous improvement.
It can be used in conjunction with identifying root causes through 5 why. 7 basic quality management tools quality management tools listed below were greatly emphasized upon by kaoru ishikawa, who was instrumental in creating total quality management and maximizing productivity by improving the quality of deliveries in the manufacturing industry.these seven basic quality management tools are also known as the. Managers must show they are committed by providing the training and implementation support necessary.
This tool helps organizations to clearly segregate their processes, activities, and events and also helps them in understanding the work efforts put in by their. These templates will help you get started using the seven basic quality tools. They are a set of relativity simple data analysis tools used to support quality improvement efforts.
The critical factors of tqm are the elements that may lead to satisfactory performance, as has been proved by other studies ( saraph et al., 1989; The american society of quality (asq) recognizes seven essential quality control tools, and these are ideal for presenting data in an understandable way so that it can be analyzed for improvement. Be possible if they are assured that management cares about improving quality.
In fact, the same tool or technique that was used in the assessment may be reused to obtain information necessary to ascertain a measurement. Brainstorming is another core member of the quality management tools suite. • problem solving methodology, such as drive • process mapping • process flowcharting
-
Does God hate me? GotQuestions.org . WebGod does not hate anyone. However, those who, by their life choices, set themselves against Hi...
-
What Is Slack Tide [2022] How Long Is It & When Does It Occur? . What Is Slack Tide? To put it simply, the slack tide is when wate...
-
They should be advised to either work overtime or arrive at work early. It is to inform you that i have inspected my new house which was bui...
watch your six
Watch Your Six Meaning, Origin & Example. . When used in combat scenarios, “watch your six” literally means “keep an eye on what’s...

ads
Search This Blog
Blog Archive
- January 2023 (3)
- November 2021 (4)
- October 2021 (22)
- September 2021 (18)
- August 2021 (25)
- July 2021 (19)
- June 2021 (23)
- May 2021 (21)
- April 2021 (18)
- March 2021 (22)
- February 2021 (20)
- January 2021 (24)
- December 2020 (16)
- November 2020 (21)
- October 2020 (18)
- September 2020 (61)
- August 2020 (1)
Labels
- abbreviated
- abbreviation
- abraham
- action
- after
- agreement
- alphabet
- among
- ancient
- annual
- another
- answer
- answers
- antonym
- appraisal
- articulation
- attract
- avoid
- avoiding
- balanced
- beginning
- behaviour
- being
- benefits
- between
- black
- bloom
- books
- bottle
- bottom
- breach
- building
- business
- called
- calling
- certificate
- chain
- challenge
- change
- character
- charles
- check
- children
- cleaner
- coaching
- common
- company
- compensation
- competence
- complaint
- computer
- concept
- concern
- conclusion
- confidence
- connotation
- conscious
- consequences
- content
- continuous
- contract
- contractor
- contrast
- corporate
- court
- crossword
- cultures
- customer
- customers
- dance
- daniel
- death
- define
- definition
- demonstrate
- describe
- description
- development
- dichotomy
- dictionary
- difference
- different
- difficult
- dimensions
- direction
- director
- disaster
- discount
- dismissal
- diversity
- does
- doors
- double
- dramatic
- during
- duties
- ehrmann
- elements
- emotional
- employee
- employer
- employment
- english
- equality
- equity
- erick
- eriksons
- ethical
- ethics
- event
- example
- examples
- executive
- explain
- explained
- explanation
- external
- failure
- family
- fashion
- features
- first
- forces
- formal
- format
- forming
- fortunes
- franchising
- french
- friends
- fundamental
- funny
- gardners
- general
- generic
- gestures
- golden
- grammar
- grave
- greek
- grievance
- groups
- handwriting
- hate
- health
- heart
- hierarchy
- hiring
- history
- horizon
- hotel
- identify
- identifying
- illustrate
- impact
- implementation
- important
- improved
- improvement
- inclusion
- incompetence
- increase
- industry
- inspirational
- intelligence
- intelligences
- interview
- introducing
- introduction
- issues
- johari
- judging
- kipling
- knackers
- knowledge
- kolbs
- landlord
- language
- latin
- leader
- leadership
- learning
- legal
- letter
- letters
- level
- long
- looking
- making
- management
- manager
- managerial
- managers
- marketing
- marks
- maslow
- matrix
- mcgregor
- meaning
- meanings
- measuring
- meeting
- meetings
- member
- mental
- metaphor
- michael
- middle
- model
- monitor
- motivation
- mouton
- multiple
- needs
- negotiation
- noise
- norming
- notice
- objectives
- obvious
- offering
- office
- online
- opportunities
- opportunity
- oracle
- orderly
- organisation
- organizational
- origin
- others
- outsourcing
- overview
- paper
- party
- perform
- performance
- person
- personal
- personality
- placidly
- planning
- porter
- porters
- poster
- powerpoint
- prefix
- presentation
- pressure
- problem
- procedure
- process
- product
- professional
- project
- promotion
- proposed
- prospective
- psychosocial
- publicity
- quality
- questionnaire
- questions
- quote
- quotes
- random
- recent
- recommendation
- redundancy
- reference
- referral
- reflection
- relations
- relationship
- report
- request
- research
- resignation
- respond
- response
- responsibilities
- responsibility
- restaurant
- retrenchment
- review
- rhyme
- rhymes
- roles
- rudyard
- sales
- sample
- schedule
- scheins
- sentence
- separation
- service
- slack
- social
- solving
- someone
- special
- spell
- stages
- stand
- statement
- stories
- storming
- strategic
- strategies
- strategy
- strength
- structure
- students
- study
- style
- styles
- suitability
- support
- sustainability
- syllogism
- tattoos
- taxonomy
- technique
- techniques
- technology
- template
- terminated
- termination
- terms
- thank
- theory
- there
- these
- third
- threat
- tide
- tools
- training
- translation
- tricks
- triumph
- trivia
- truck
- tuckman
- types
- unconscious
- understanding
- universal
- uppercase
- verbal
- verification
- wanna
- watch
- weakness
- window
- without
- words
- worker
- worksheet
- write
- writing
- your